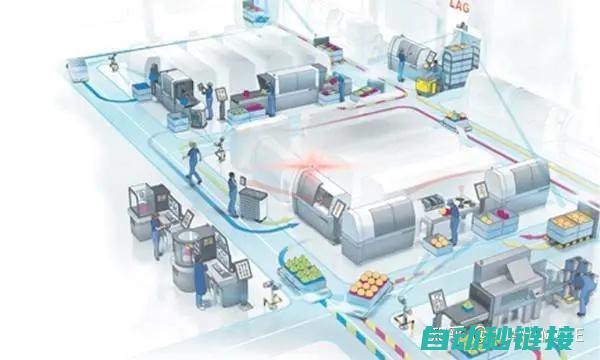
一、引言
PLC(可编程逻辑控制器)作为一种重要的工业控制装置,广泛应用于各种自动化生产领域。
PLC程序设计是确保PLC正常运行的关键环节,本文将详细介绍PLC程序设计的流程,帮助读者更好地理解和应用。
二、需求分析
1. 明确控制任务:在进行PLC程序设计之前,首先要明确控制任务,了解生产过程中的具体需求,如控制对象、控制要求等。
2. 调研现场情况:设计师需要深入生产现场,了解实际生产环境、设备布局、信号类型及范围等情况,为后续的PLC程序设计提供基础数据。
3. 制定设计方案:根据需求分析和现场调研结果,制定详细的设计方案,包括PLC选型、硬件配置、软件配置等。
三、硬件设计
1. PLC选型:根据实际需求选择合适的PLC型号,考虑因素包括CPU性能、内存容量、通信接口等。
2. I/O模块配置:根据现场信号类型及范围,配置相应的输入/输出模块,实现信号转换和传输。
3. 扩展模块选择:根据实际需求选择相应的扩展模块,如定位控制模块、温度控制模块等。
4. 接线与布局:根据PLC及其模块的布局,进行接线设计,确保电气连接正确、可靠。
四、软件设计
1. 编程环境选择:选择合适的PLC编程软件,如西门子TIA Portal、欧姆龙CX-Programmer等。
2. 程序设计语言:根据实际需求选择合适的程序设计语言,如梯形图、功能块图、结构化文本等。
3. 程序结构设计:根据控制任务,将程序划分为若干模块,如主程序、子程序、中断程序等,便于后期调试和维护。
4. 功能实现:根据设计方案,实现各项功能,包括数据处理、逻辑控制、运动控制等。
五、程序编写与调试
1. 程序编写:根据软件设计结果,使用选定的编程环境进行程序编写。
2. 仿真调试:在程序编写完成后,进行仿真调试,检查程序逻辑是否正确。
3. 现场调试:将编写好的程序下载到PLC中,进行现场调试,验证程序的实用性。
4. 问题处理:在调试过程中,如发现程序存在问题,需及时修改并重新调试,确保程序正常运行。
六、优化与完善
1. 性能优化:在保证程序功能的前提下,对程序进行优化,提高PLC的运行速度和响应性能。
2. 可读性提高:对程序进行注释、命名等处理,提高程序的可读性,便于后期维护。
3. 兼容性考虑:在程序设计过程中,要考虑与其他设备的兼容性,确保整个系统的稳定运行。
4. 安全性保障:在程序中加入安全机制,如故障检测、安全停止等,提高系统的安全性。
七、文档编写与验收
1. 文档编写:在PLC程序设计过程中,需要编写相应的文档,包括设计说明书、调试记录、使用手册等。
2. 验收标准制定:根据实际需求制定验收标准,包括功能验收、性能验收、安全验收等。
3. 验收与整改:按照验收标准对PLC程序进行验收,如存在问题,需进行整改并重新验收。
4. 交付使用:验收合格后,将PLC程序及相关文档交付给使用部门,进行实际运行。
八、总结与展望
本文详细介绍了PLC程序设计的流程,包括需求分析、硬件设计、软件设计、程序编写与调试、优化与完善以及文档编写与验收等环节。
在实际应用中,需要根据具体情况进行灵活调整,不断提高PLC程序设计的水平,以满足不断变化的工业控制需求。
未来,随着工业自动化水平的不断提高,PLC程序设计将面临更多的挑战和机遇,需要设计师们不断学习和创新,为工业发展做出更大的贡献。
发表评论